Many industries today rely heavily on outsourced manufacturing. From automobiles and machineries to electronics and consumer goods, an estimated 70 to 80% of all manufacturing activities are outsourced. It has become the status quo for companies to trust external partners and suppliers with their manufacturing processes. However, many businesses face unexpected challenges when suppliers fail to deliver quality products, and find it difficult to collaborate with their suppliers on operational improvements.
Such challenges stem from a lack of transparency. In the current landscape, where OEMs have minimal visibility into their suppliers’ operations, manufacturing leaders often become aware of issues only after they have already disrupted production. This reactive approach results in delays, quality issues, and inefficiencies that can significantly impact a company’s output, revenue, and even reputation.
The Status Quo of Outsourced Manufacturing
In today’s outsourced manufacturing environment, transparency and collaboration between OEMs and suppliers remain limited. After negotiating a contract, both parties rely on its terms to govern the relationship, assuming mutual trust will ensure smooth operations. This reliance on trust has shaped industry dynamics for decades, becoming an accepted norm rather than an actively managed process.
While this may seem like a balanced and cooperative approach, in reality, it often leads to long-term breakdowns in communication and partnership.
A 2023 survey by the Capgemini Research Institute1 highlights this challenge, revealing that 71% of manufacturing professionals cite a lack of trust between OEMs and suppliers as a major barrier to information sharing. Additionally, 55% of suppliers feel that OEMs fail to treat them as equal partners – a sentiment that rises to 75% in China. These figures underscore the urgent need for greater transparency in manufacturing supply chains.


The Hidden Risks from the Status Quo
In this kind of contract-driven relationship, OEMs face multiple risks.
Late delivery. Delayed part deliveries have an immediate and substantial impact on assembly line operations, directly disrupting production schedules and revenue streams. In the automotive industry, where a single factory produces approximately 1,000 vehicles per day, even a one-day delay can translate into staggering financial losses. Assuming an average vehicle price of $30,000, a full-day production halt equates to a staggering $30 million in lost revenue.
Unseen cost drains. For suppliers to produce parts for OEMs, they require the corresponding tooling assets, such as molds and dies. To facilitate this, OEMs provide these toolings to their suppliers, operating on the assumption that they will be used efficiently and responsibly.
In practice, tooling assets are often underutilized and poorly maintained by suppliers – yet OEMs remain largely unaware of these cost drains. Suppliers prioritize meeting production demands and typically lack incentives to maximize tooling efficiency. As a result, they frequently request more toolings than necessary, leading to CapEx hikes and misplaced assets. Under the current system, suppliers are also less inclined to extend the lifespan of existing toolings through proper maintenance. Instead, they opt to scrap tools that require upkeep and order replacements, driving up costs and contributing to unnecessary waste – all of which the OEMs are not aware of.
Quality issues. Supplier mismanagement can significantly impact parts quality, leading to defects, scrap, and increased costs. One common issue is tooling overload – when suppliers push their toolings beyond their capacity to meet production targets. This overuse shortens the tooling’s lifespan and results in defective parts. Additionally, delayed or reactive tooling maintenance further contributes to quality degradation, increasing the likelihood of faulty components and unnecessary waste.
For OEMs, closely monitoring every part for quality issues is neither practical nor cost-effective. As a result, many defects go unnoticed until they cause larger production setbacks or customer dissatisfaction.
Poor decision making. Without clear visibility and quantitative data on supplier performance, OEMs often rely solely on contract fulfillment as their primary evaluation metric. Over time, this lack of data-driven decision-making leads OEMs to select suppliers based on familiarity and past relationships rather than objective performance insights. This approach, while convenient, is neither logical nor optimal, as it fails to identify high-performing suppliers and address systemic problems.
Defying Industry Norm: Trust and Transparency Go Hand in Hand
Clearly, the biggest flaw of the industry norm is the lack of transparency. OEMs place blind trust in their suppliers, expecting results without actively engaging in operational improvements or tooling maintenance. Over time, this passive approach weakens the relationship, especially when late deliveries and quality issues arise. Since switching suppliers is both costly and disruptive, OEMs and suppliers often settle into a state of minimal satisfaction – maintaining the status quo rather than striving for real improvements. This stagnation prevents meaningful progress, leaving inefficiencies, quality issues, and operational bottlenecks unaddressed.
The Critical Role of Outsourced Manufacturing Monitoring
eMoldino empowers manufacturers with real-time visibility into their outsourced manufacturing processes by equipping molds and dies with IIoT sensors. These sensors track tooling data in real-time, such as location, uptime, shot count, cycle time, and temperature, ensuring manufacturers have complete oversight of their tooling assets.
With the collected data, eMoldino leverages advanced analytics to conduct predictive maintenance forecasts and send alerts to both OEMs and suppliers, enabling proactive servicing before tools reach their maintenance threshold. On average, this approach extends tooling lifespan by 40%, reducing unexpected failures and downtime.
Beyond tooling management, eMoldino also quantifies production data within supplier factories. By analyzing shot counts and cycle times, it accurately calculates Overall Equipment Effectiveness (OEE), allowing manufacturers to assess supplier performance with data-driven precision and make more informed sourcing decisions.
For more information on tooling asset management and outsourced manufacturing monitoring, visit emoldino.com or request a demo.
1 Capgemini Research Institute (2023) “Automotive Supply Chain: Pursuing Long-Term Resilience”
About the author
eMoldino
eMoldino aims to digitalize, streamline, and transform your manufacturing and supply chain operations. We help global manufacturers who want to drive corporate innovation while maintaining the core values of collaboration and sustainability. Talk with us to learn more →
Did you enjoy reading this article?
0 / 5. Vote count: 0
Explore Our Latest Posts
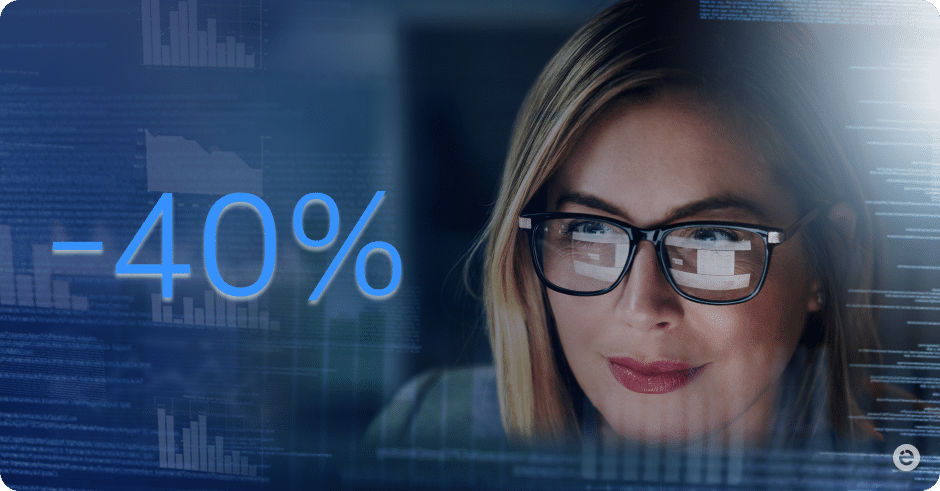
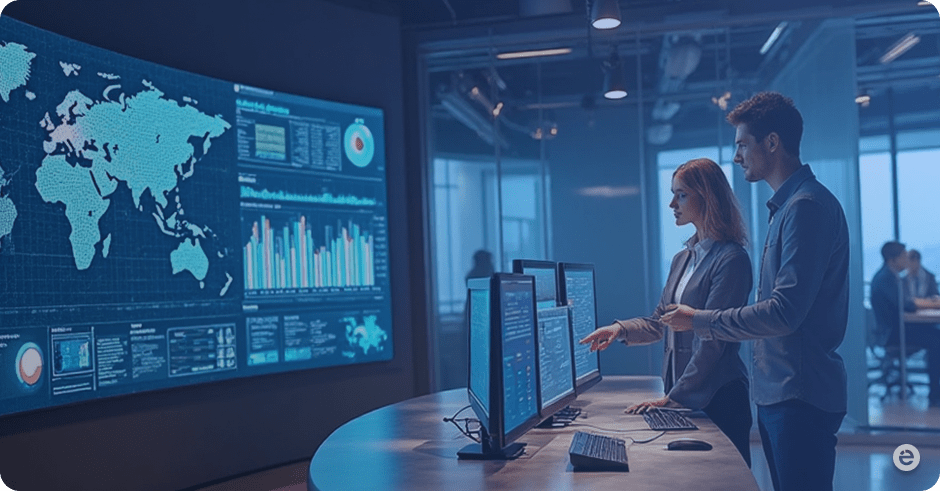
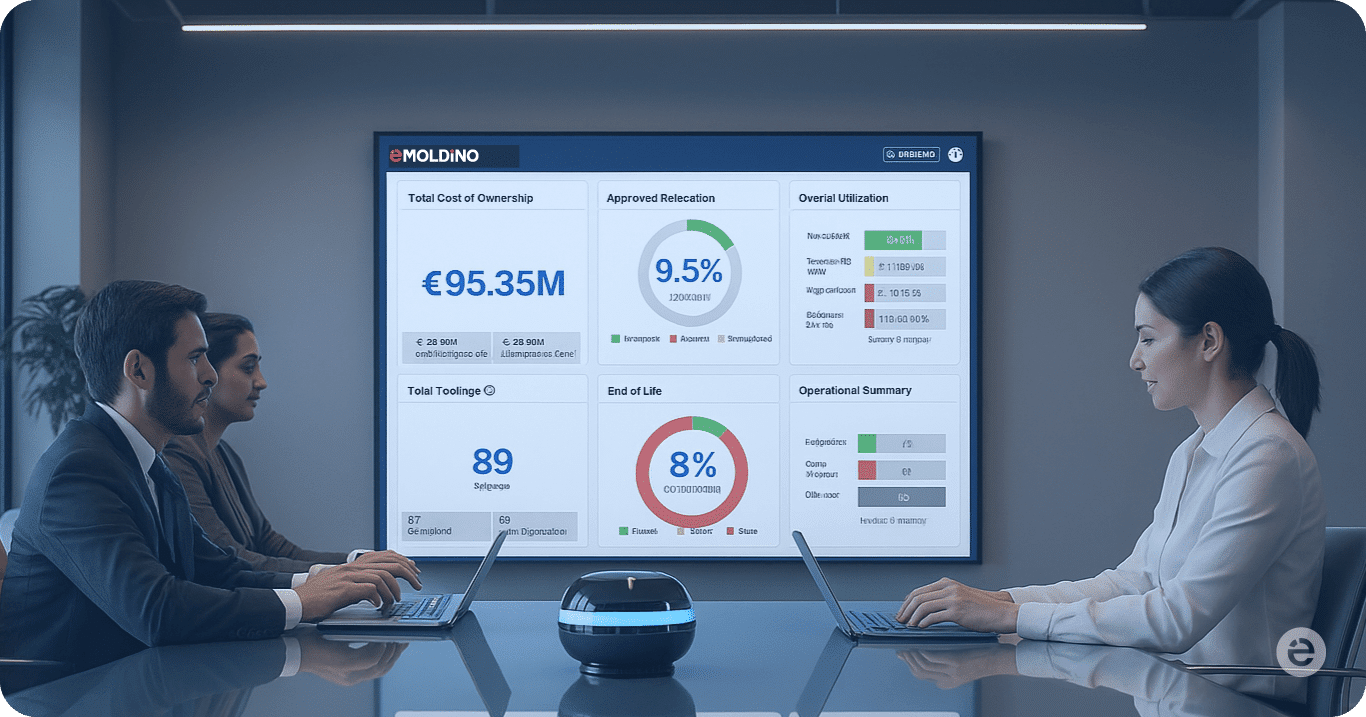
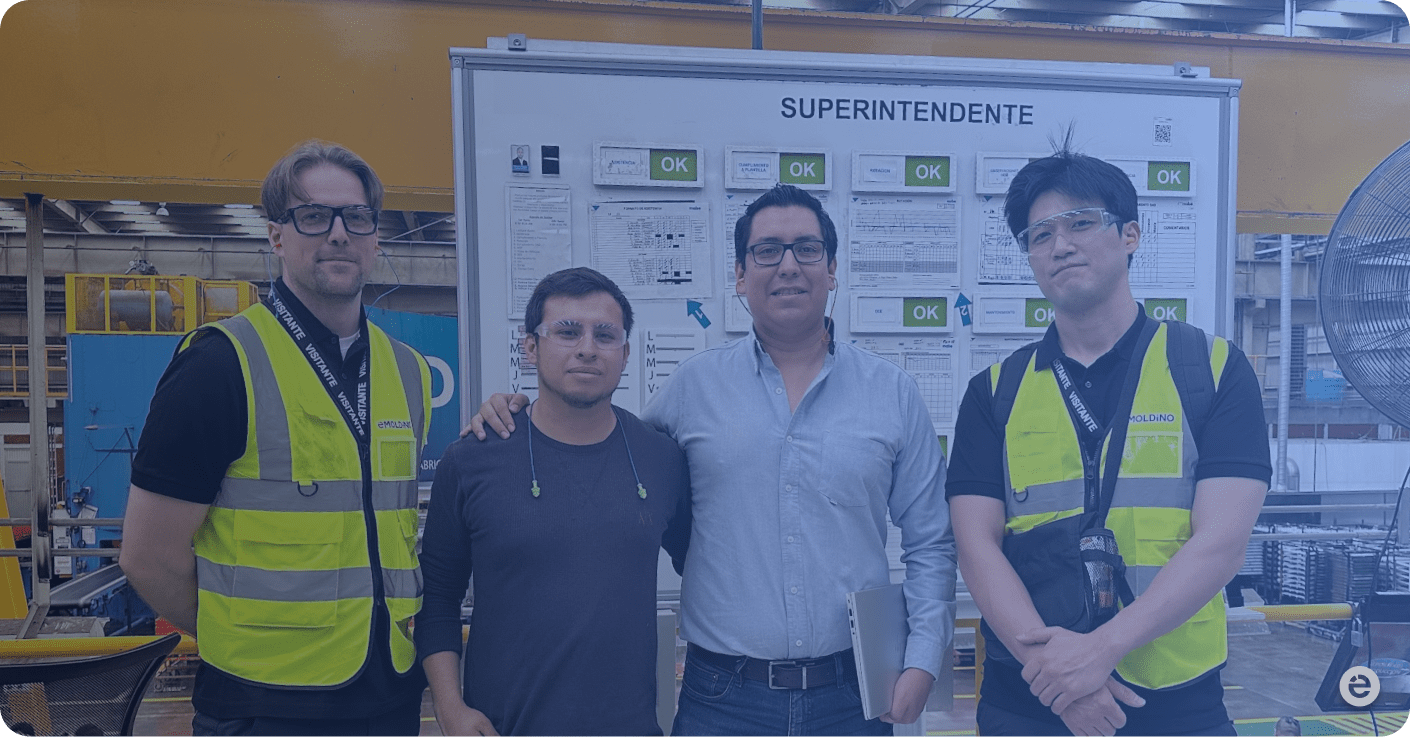
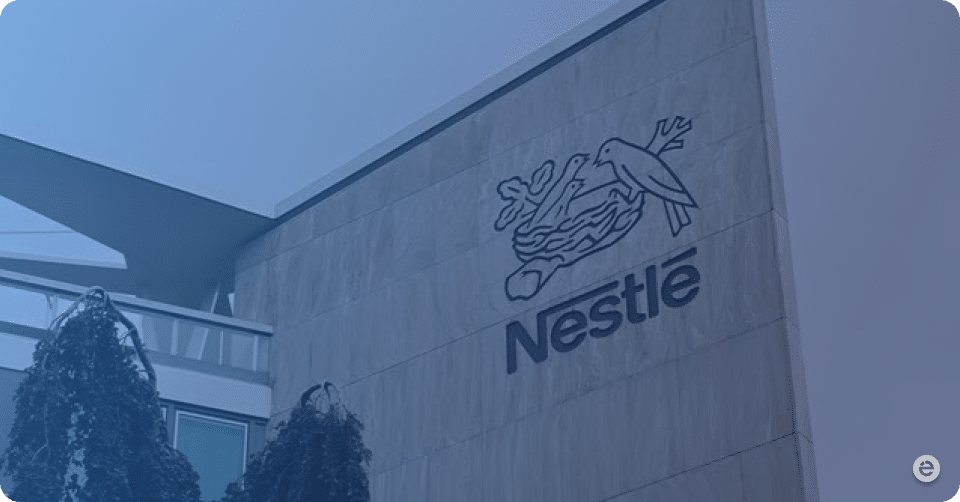
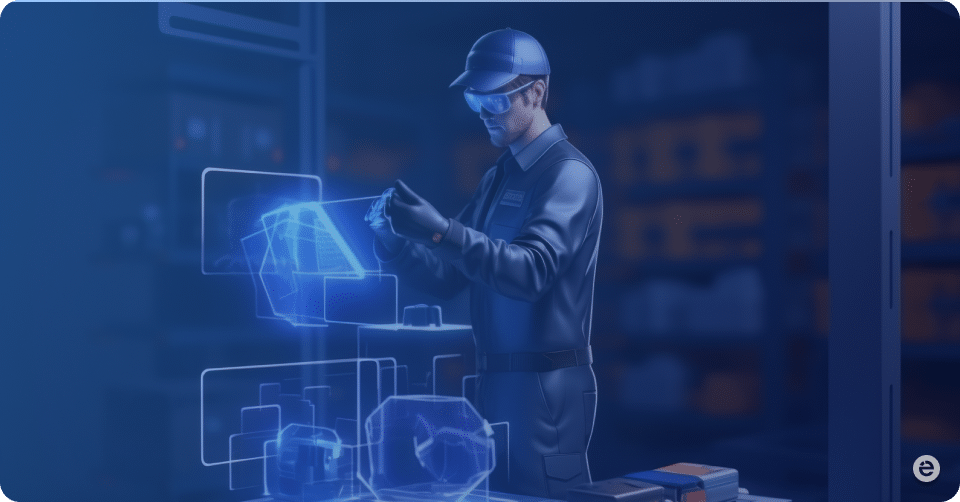
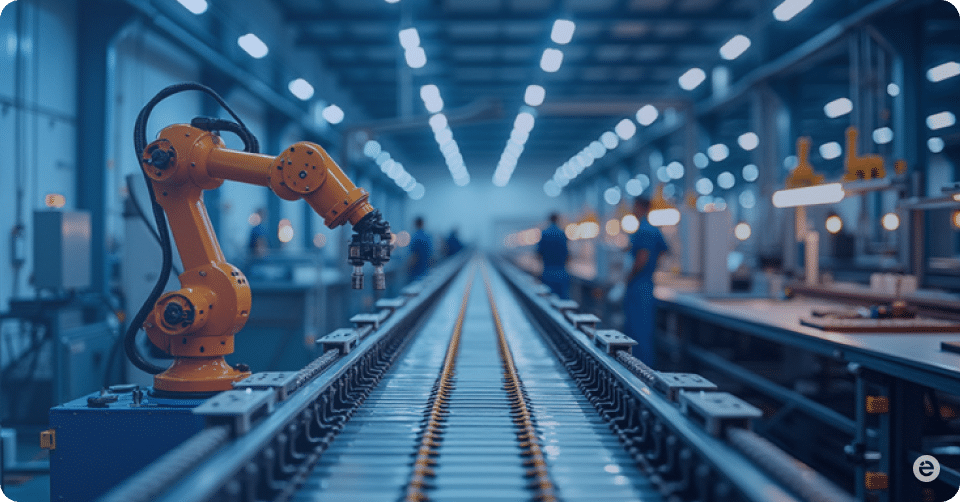
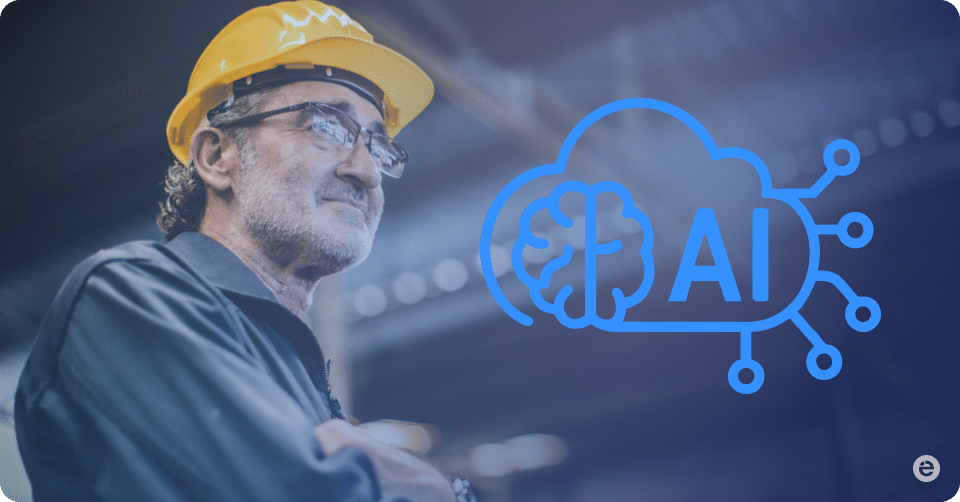
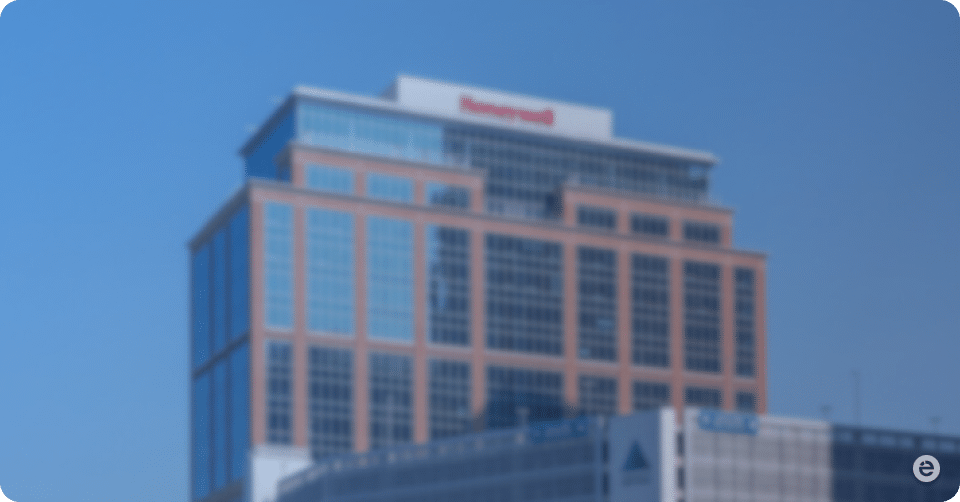
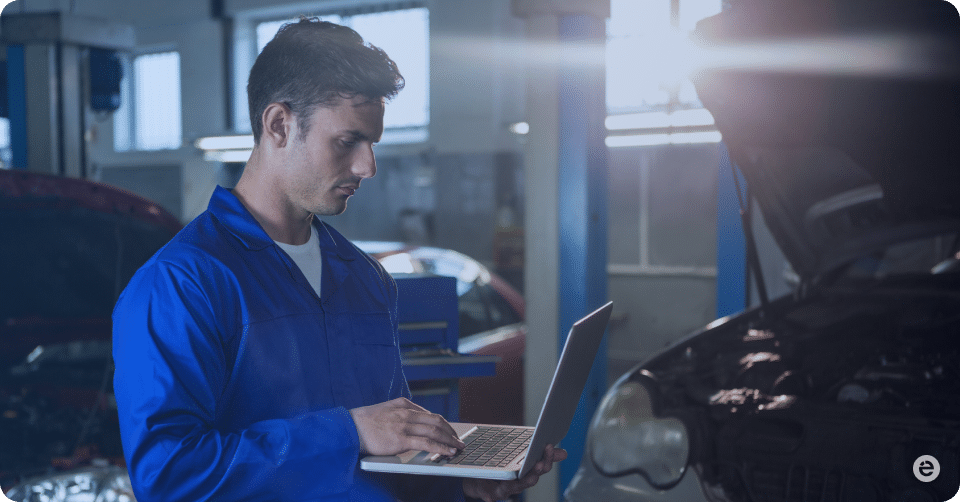
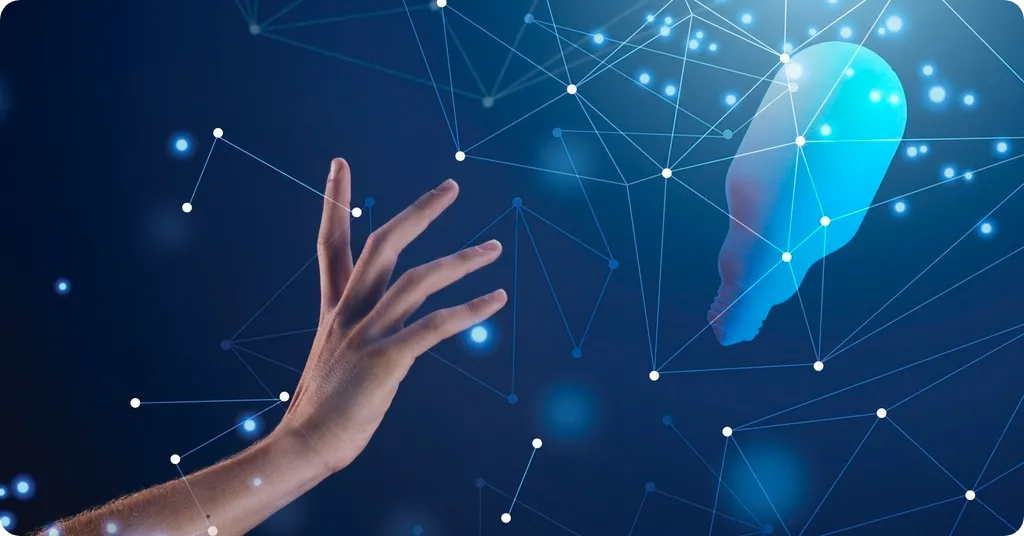