Outsourced manufacturing has become the global standard for speed, scalability, and cost-efficiency. From automotive to consumer electronics, companies rely heavily on third-party suppliers—often spread across continents—to meet aggressive production targets.
But with this globalized model comes a new challenge: lack of visibility and control.
When production is outsourced, manufacturers lose real-time insight into how parts are being made, how tools are performing, and whether suppliers are meeting quality and efficiency standards. This creates a vulnerable supply chain—prone to delays, defects, and disruption.
At eMoldino, we believe the key to restoring control and building resilience in outsourced manufacturing lies in an overlooked but critical asset: your tooling.
Why Tooling Matters More Than Ever in Outsourced Production
Tooling—particularly molds used in injection molding—is at the heart of manufacturing quality, speed, and consistency. Yet when manufacturing is outsourced, most OEMs have little to no visibility into how their tools are being used, maintained, or moved.
This “black box” model causes several risks:
- Unplanned tool failure halting production
- Undocumented tooling transfers between suppliers
- Undetected overuse or misuse leading to quality issues
- Difficulty tracing defects back to tool performance
A single undetected defect or late shipment can ripple across your supply chain. In an era where customer expectations are high and penalties are steep, that’s a risk businesses can’t afford.
The New Model: Data-Driven Oversight of Outsourced Tooling
With eMoldino’s smart tooling solution, manufacturers gain real-time visibility and control over outsourced tooling, even when it’s operated by external partners across the globe.
Our IoT devices are installed directly on each mold, tracking critical metrics like:
- Production cycle count
- Operating location (GPS-enabled)
- Downtime and tool idle time
- Maintenance history
- Predictive wear indicators
All this data is automatically fed into our centralized platform, where you can monitor tooling performance by supplier, region, or production line.
You no longer have to rely on monthly Excel reports or reactive quality checks. You have truth in real time.
4 Ways Smart Tooling Data Builds Resilience in Outsourced Manufacturing
1. Ensure Global Traceability of Tools
Many OEMs lose track of where their tools physically are—especially when they’re transferred between Tier 1 and Tier 2 suppliers. This creates delays and security risks.
eMoldino’s platform provides GPS-level Real-time visibility of your toolings worldwide, helping you:
- Prevent unauthorized transfers
- Maintain compliance with tooling ownership policies
- Ensure tools are deployed where demand is highest
✅ Result: Better asset control and faster response to shifting production needs.
2. Hold Suppliers Accountable with Performance Data
When production is outsourced, supplier self-reporting often lacks transparency. With eMoldino, you gain objective, real-time data on supplier tool usage and output.
You can:
- Benchmark supplier productivity
- Detect tool misuse or overload
- Automate monthly tooling performance scorecards
This data creates a fact-based dialogue with suppliers—transforming relationships from reactive to collaborative.
✅ Result: Improved supplier accountability and stronger partnerships.
3. Prevent Production Disruptions with Predictive Maintenance
Outsourced suppliers may skip preventive maintenance to save time or costs—until tools break down, causing weeks of lost production.
eMoldino enables predictive maintenance through real-time wear analysis and usage trends, alerting you and your suppliers before a failure occurs.
✅ Result: Reduced downtime, smoother delivery schedules, and better planning.
4. Standardize Part Quality Across All Locations
When multiple suppliers produce the same part using the same tool, quality inconsistencies are common. eMoldino’s tooling insights help you identify subtle deviations in tool performance across sites.
You can:
- Detect early signs of wear impacting quality
- Cross-compare tool performance across suppliers
- Maintain consistent part quality regardless of location
✅ Result: Fewer defects, stronger compliance with OEM standards, and fewer customer complaints.
A Real-World Impact: From Reactive Oversight to Proactive Control
One of our clients, a global automotive supplier, struggled with inconsistent part quality from its Asia-based tool suppliers. With over 1,500 tools in operation across 7 countries, oversight was nearly impossible.
After implementing eMoldino, they gained:
- 100% tooling traceability
- 30% reduction in tool-related downtime
- Faster root cause analysis for defects
- Clear supplier performance benchmarking
Now, they don’t just outsource production—they manage it intelligently.
Final Thoughts: Data Is the New Currency of Control
Outsourced manufacturing isn’t going away. In fact, it’s growing. But the companies that win in this environment won’t be the ones that simply cut costs. They’ll be the ones that stay in control—with real-time data, intelligent systems, and predictive insights.
At eMoldino, we help manufacturers build resilient, intelligent supply chains by starting at the source: the tooling. Whether you’re managing 200 molds or 2,000, our platform helps you operate smarter, collaborate better, and deliver more consistently—everywhere.
Ready to transform your outsourced supply chain from reactive to resilient?
About the author
eMoldino
eMoldino aims to digitalize, streamline, and transform your manufacturing and supply chain operations. We help global manufacturers who want to drive corporate innovation while maintaining the core values of collaboration and sustainability. Talk with us to learn more →
Did you enjoy reading this article?
0 / 5. Vote count: 0
Explore Our Latest Posts
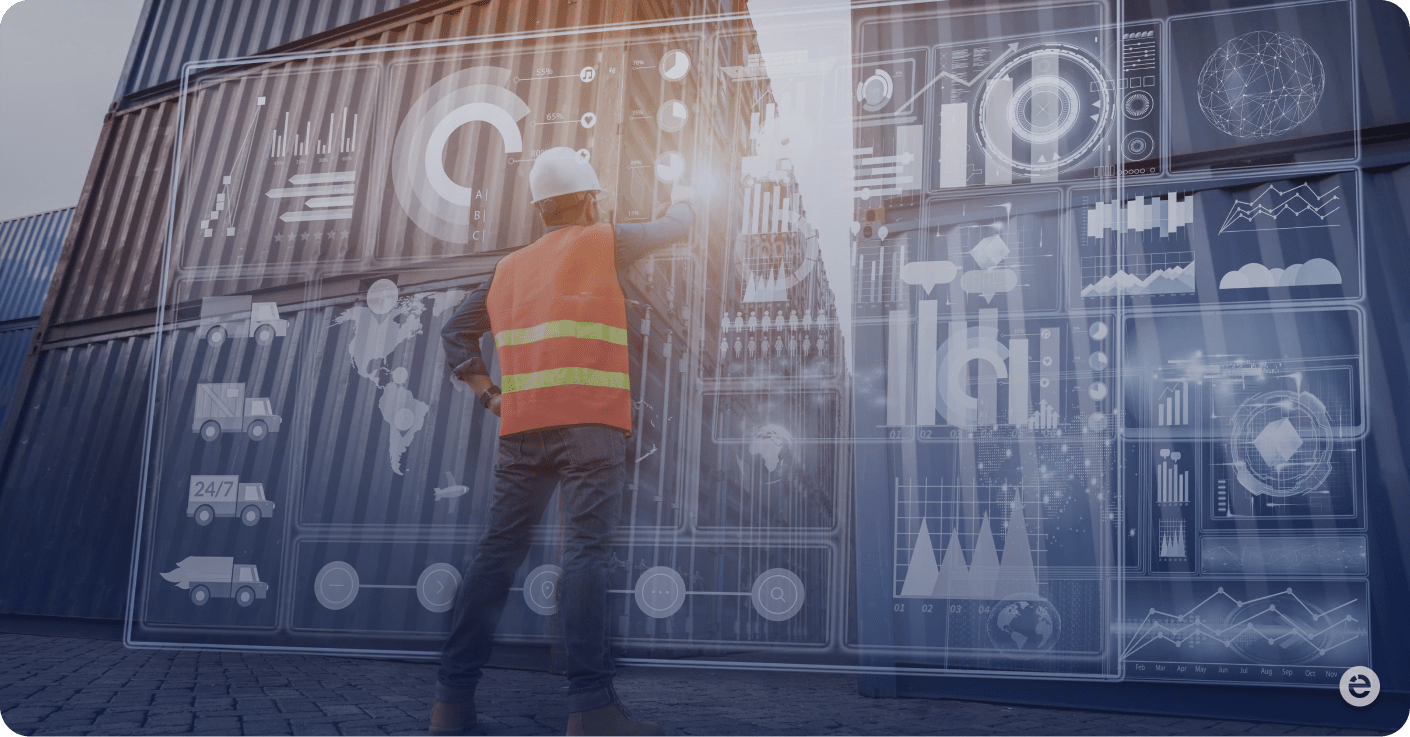
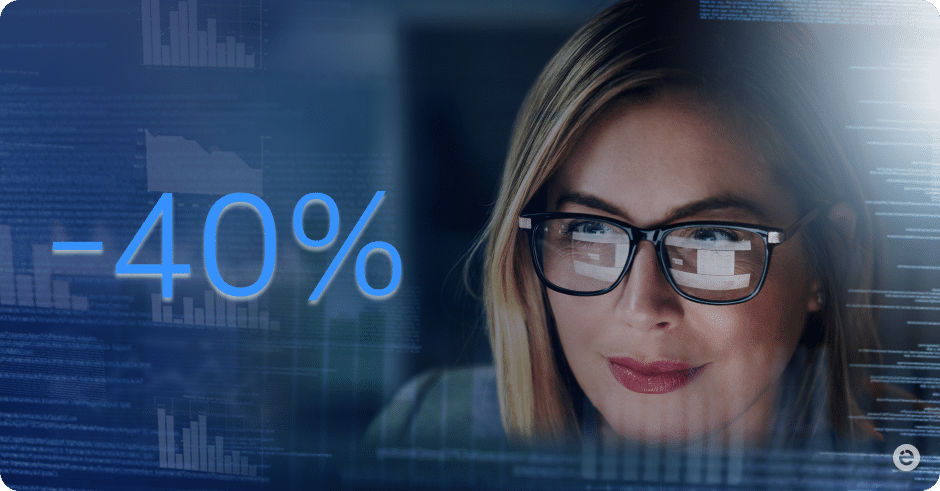
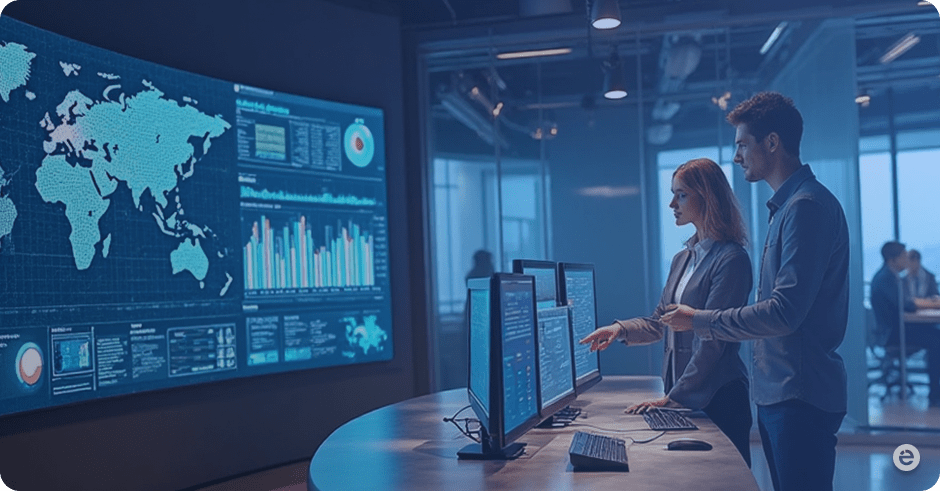
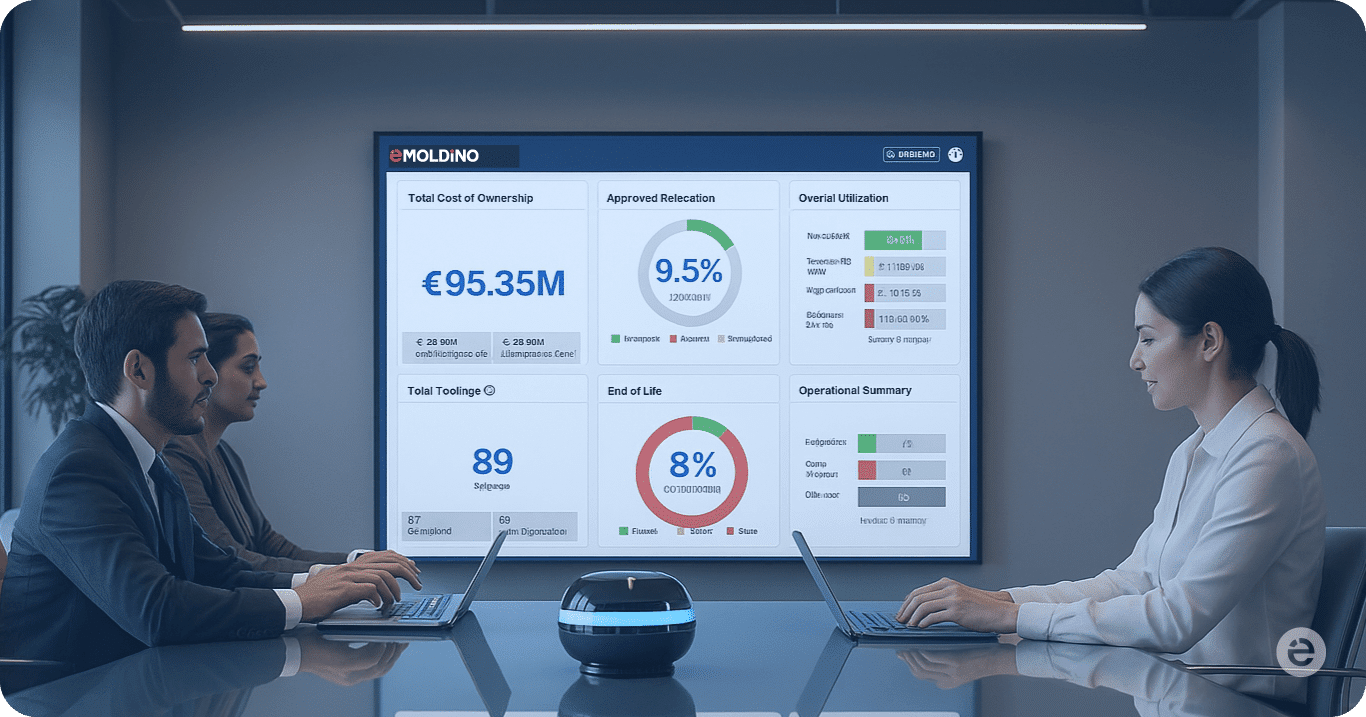
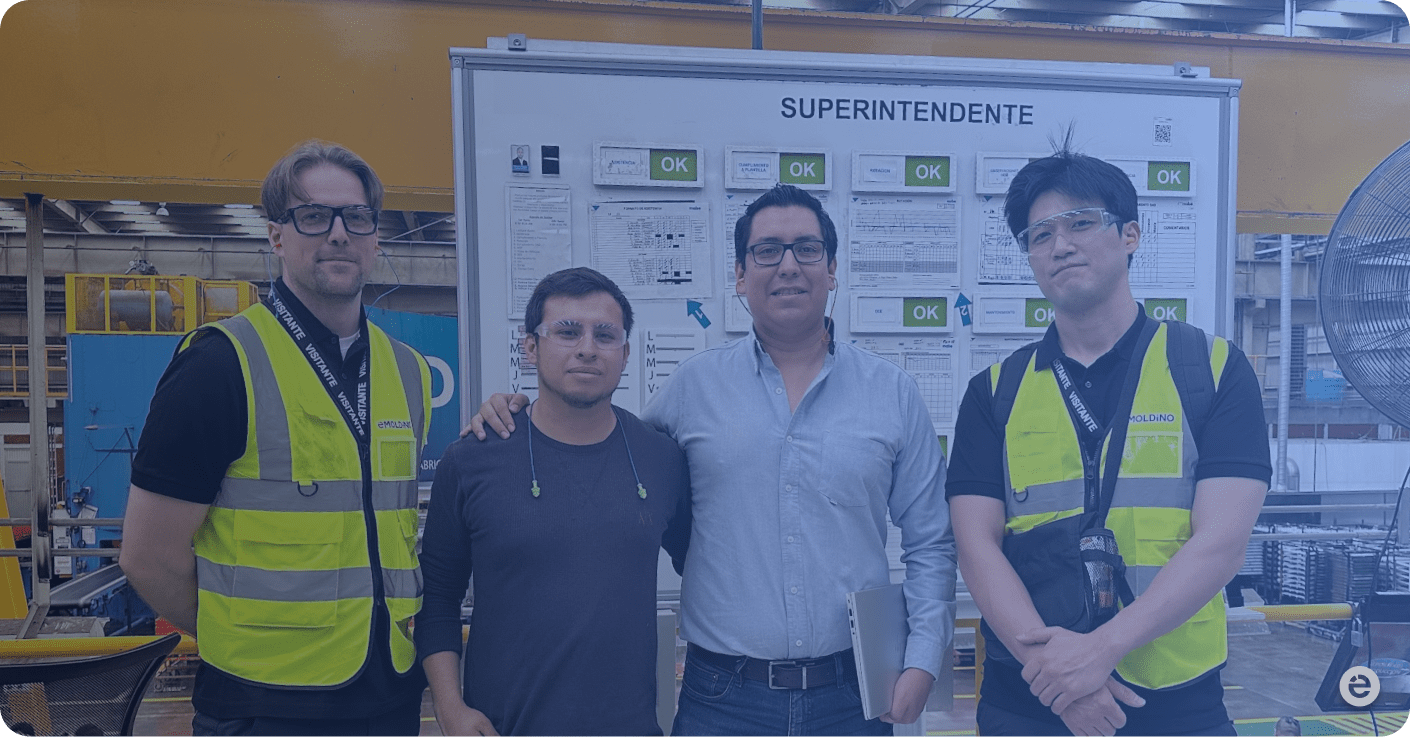
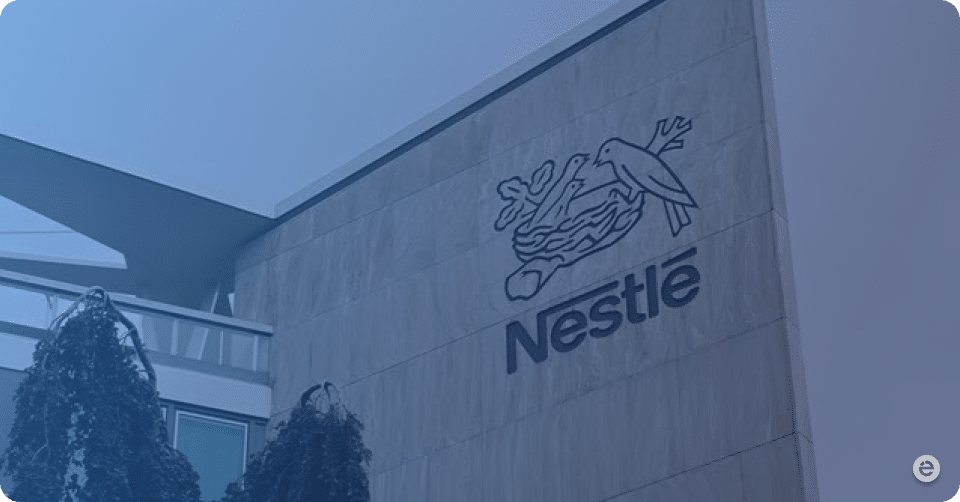
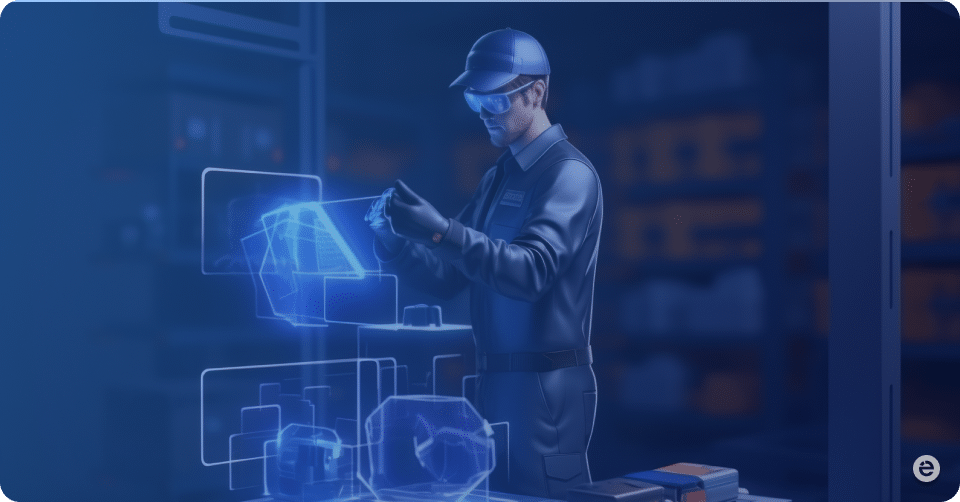
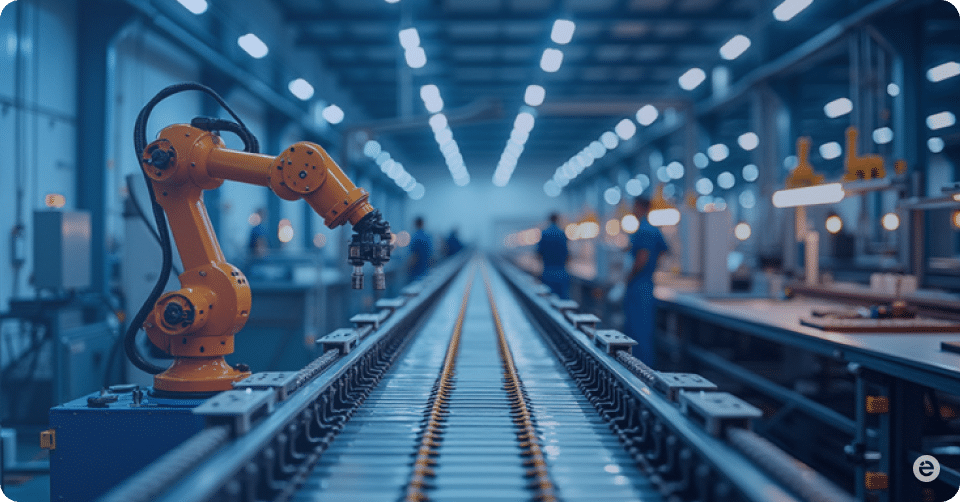
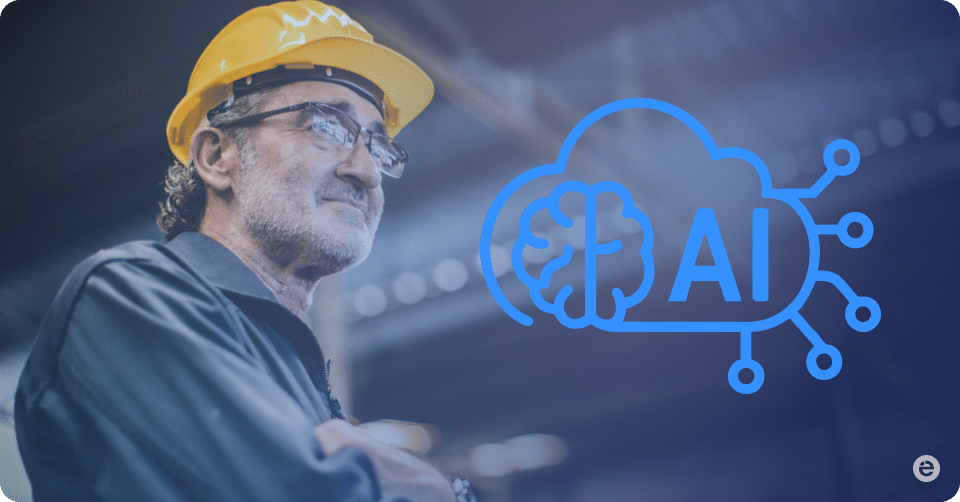
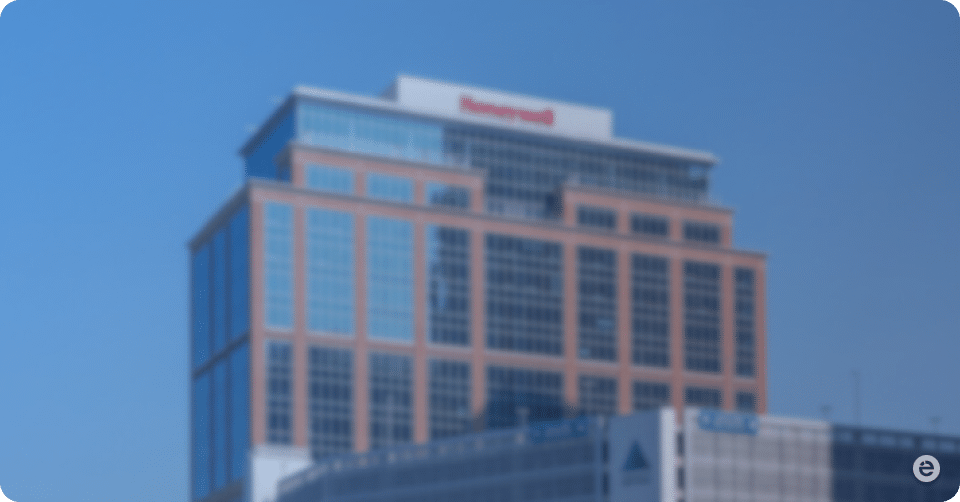
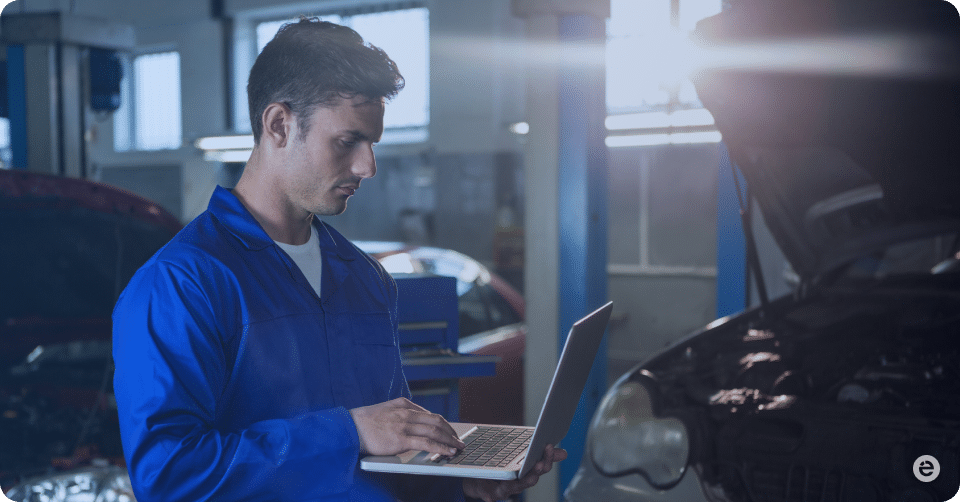